News Summary
Ajax Paving of Florida has enhanced its operational efficiency by integrating advanced construction management software, B2W. This software optimizes work orders, inventory management, and scheduling while reducing costs and time. The company now utilizes real-time insights for parts management, streamlined procurement, and improved inventory management, resulting in a significant decrease in operational inefficiencies. Innovative delivery methods and revised inspection protocols also play a crucial role in Ajax’s commitment to efficiency. These advancements are set to position the company strongly in the competitive construction industry.
Ajax Paving of Florida Boosts Efficiency with New Software
Ajax Paving of Florida has taken a significant step toward enhancing its operational efficiency by incorporating advanced construction management software into its daily operations. This technological upgrade is designed to streamline processes, leading to substantial time and cost savings in various aspects of the company’s operations.
Operational Improvements
The implementation of this new software, known as B2W, has fundamentally transformed aspects like work orders, parts inventory, and service scheduling. By utilizing the software, Ajax is now able to gain real-time insights into parts ordering and machine maintenance issues. This move is expected to provide the company with a competitive edge in the construction industry.
Effective Parts Management
Previously, Ajax faced ongoing challenges with recurring parts orders approximately every 90 days, which triggered a thorough analysis of the underlying issues. With the new software, technicians now access an app to order parts, effectively streamlining the procurement process. All parts requests are routed through centralized purchasing at the main warehouse, allowing for quicker and more accurate orders.
Ajax’s inventory management system is structured so that 95% of its parts are held in one main warehouse, while several satellite locations maintain stock of fast-moving items. This setup not only ensures that critical parts are readily available but also empowers mechanics to submit direct requests to vendors, reducing the time spent on procurement significantly.
Enhanced Communication and Inspection Processes
The software has improved communication channels within the organization, minimizing inefficiencies and the occurrence of incorrect parts orders. Mechanics are only dispatched to inspect repair requests when there is insufficient information provided in the initial submission. This refined process has led to a decrease in unnecessary mechanical inspection trips, translating to considerable savings in travel time.
The new app used by technicians also provides updates on the status of parts orders, informing them when items are in transit or have been delivered. Furthermore, an innovative Uber Eats-style delivery option for parts has been launched, using couriers for deliveries instead of relying on dedicated parts runners.
Revising Inventory Strategies
A key focus of Ajax has been the historical challenges associated with overstocking parts due to a fear of shortages. Following an extensive review of inventory levels, the company executed strategy changes that resulted in a significant $100,000 reduction in total inventory costs. Despite lowering overall inventory levels to around $500,000, Ajax improved the number of available line items, ensuring that essential components remain accessible.
Operational Efficiency Gains
The company’s ability to close work orders efficiently has notably improved due to better management of parts inventory. Ajax now prioritizes lead times for parts delivery and determines what to stock based on their availability. A ranking system has been introduced to provide heightened attention to critical parts necessary for uninterrupted operations.
The visibility within Ajax’s operations has increased, resulting in more effective scheduling and reporting that enhances overall performance across the board. Additionally, reports on preventative maintenance (PM) are accessible to all employees, which reduces dependency on individual data management and fosters a more collaborative working environment.
Conclusion
In summary, by embracing advanced construction management software, Ajax Paving of Florida has successfully streamlined its systems, improved communication, and enhanced information accessibility, all of which contribute to better operational efficiency. These transformative efforts position Ajax favorably within the competitive landscape of the construction industry, paving the way for future successes in project execution and resource management.
Deeper Dive: News & Info About This Topic
Additional Resources
- Construction Equipment: Ajax Paving Software
- Wikipedia: Construction Management
- PR Newswire: Murphy Tractor and Trimble
- Google Search: Construction Management Software
- Minute Hack: Digital Transformation in Heavy Equipment
- Encyclopedia Britannica: Construction Technology
- For Construction Pros: Leica Geosystems AI System
- Google News: Construction Technology
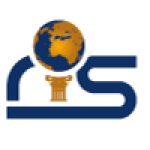
Author: Construction NY News
NEW YORK STAFF WRITER The NEW YORK STAFF WRITER represents the experienced team at constructionnynews.com, your go-to source for actionable local news and information in New York and beyond. Specializing in "news you can use," we cover essential topics like product reviews for personal and business needs, local business directories, politics, real estate trends, neighborhood insights, and state news affecting the area—with deep expertise drawn from years of dedicated reporting and strong community input, including local press releases and business updates. We deliver top reporting on high-value events such as the New York Build Expo, infrastructure breakthroughs, and cutting-edge construction technology showcases. Our coverage extends to key organizations like the Associated General Contractors of New York State and the Building Trades Employers' Association, plus leading businesses in construction and real estate that power the local economy such as Turner Construction Company and CMiC Global. As part of the broader network, including constructioncanews.com, constructiontxnews.com, and constructionflnews.com, we provide comprehensive, credible insights into the dynamic construction landscape across multiple states.